当前位置:网站首页>Airiot IOT platform enables the container industry to build [welding station information monitoring system]
Airiot IOT platform enables the container industry to build [welding station information monitoring system]
2022-07-06 18:51:00 【InfoQ】
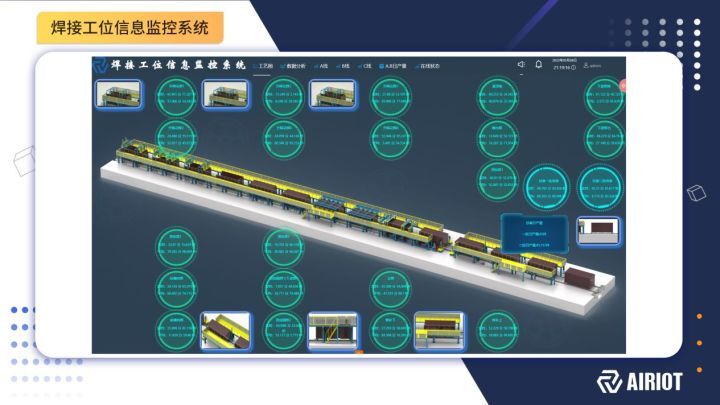
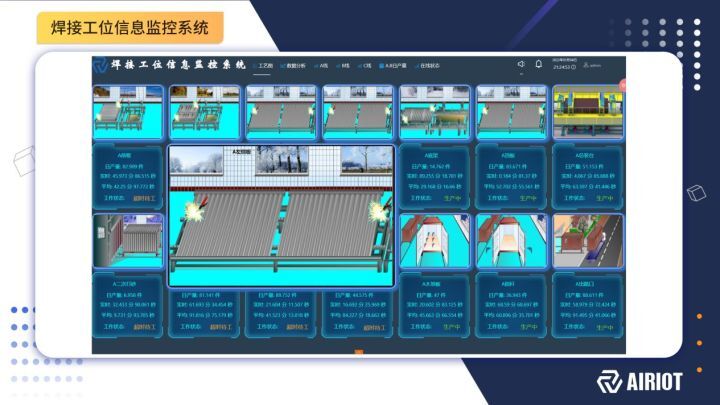
边栏推荐
- Collection of penetration test information -- use with nmap and other tools
- How are you in the first half of the year occupied by the epidemic| Mid 2022 summary
- 用于远程医疗的无创、无袖带血压测量【翻译】
- When visual studio code starts, it prompts "the code installation seems to be corrupt. Please reinstall." Solution to displaying "unsupported" information in the title bar
- 爬虫玩得好,牢饭吃到饱?这3条底线千万不能碰!
- Use cpolar to build a business website (1)
- Epoll () whether it involves wait queue analysis
- CSRF漏洞分析
- 一种用于夜间和无袖测量血压手臂可穿戴设备【翻译】
- node の SQLite
猜你喜欢
This article discusses the memory layout of objects in the JVM, as well as the principle and application of memory alignment and compression pointer
How are you in the first half of the year occupied by the epidemic| Mid 2022 summary
C#/VB.NET 给PDF文档添加文本/图像水印
Helm deploy etcd cluster
监控界的最强王者,没有之一!
测试行业的小伙伴,有问题可以找我哈。菜鸟一枚~
Penetration test information collection - CDN bypass
【论文笔记】TransUNet: Transformers Make StrongEncoders for Medical Image Segmentation
手写一个的在线聊天系统(原理篇1)
Tree-LSTM的一些理解以及DGL代码实现
随机推荐
2022.2.12
Introduction to the use of SAP Fiori application index tool and SAP Fiori tools
Some recruitment markets in Shanghai refuse to recruit patients with covid-19 positive
Visual Studio Code启动时提示“Code安装似乎损坏。请重新安装。”、标题栏显示“不受支持”信息的解决办法
SQL injection - access injection, access offset injection
Blue Bridge Cup real question: one question with clear code, master three codes
Unity资源顺序加载的一个方法
Easy to use PDF to SVG program
Reptiles have a good time. Are you full? These three bottom lines must not be touched!
Implementation of AVL tree
Describe the process of key exchange
Interpreting cloud native technology
Self supervised heterogeneous graph neural network with CO comparative learning
Atcoder a mountaineer
[Sun Yat sen University] information sharing of postgraduate entrance examination and re examination
Stm32+hc05 serial port Bluetooth design simple Bluetooth speaker
Collection of penetration test information -- use with nmap and other tools
Nuc11 cheetah Canyon setting U disk startup
10、 Process management
Specify flume introduction, installation and configuration